Automotive & Transportation
No Green Transition without Mass Balance
No Green Transition without Mass Balance
“Changing the physical properties of your output can trigger significant changes across the entire value chain. Normally, there would be a time-consuming process of testing and accepting the changed physical properties of new, more circular products and thereby innovations take time to penetrate the market. By using the biomass balance or the ChemCycling® approach, we can ensure that the physical properties of our sales products will be exactly the same as they were before and offer solutions with circular feedstocks that can be immediately used today.” – Jenny Reuber, Expert Corporate Sustainability Strategy, BASF
The shift in the automotive industry towards a more sustainable future is driving forward innovative approaches across the entire auto value chain. The industry continues to transition into an electrification of powertrain systems and concepts. At the same time, there is an opportunity to reevaluate how to make every step of the production process more sustainable, not just the batteries that power the vehicle.
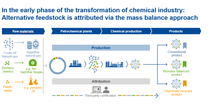
The Mass Balance Approach
One method to achieve this is the mass balance approach, which in this context means that renewable or recycled feedstock is partially replacing classical fossil feedstock at the beginning of the large and integrated value chain. This is then attributed to the end product according to the certified mass balance method. This attribution principle offers several advantages: It reduces the consumption of fossil feedstock and, depending on the specific circular feedstock, may strongly reduce the greenhouse gas emissions, all while maintaining the quality and properties of the final product. As a result, the products can be processed exactly like conventionally manufactured materials. Therefore, for the customer, there is no need to adapt formulations, plants or processes. It offers the same property and the same processing, but with a certified sustainable impact today. That is what mass balance offers.
In the case of carbon-containing feedstock, two circular versions are currently applied: one involves recycled/waste plastics, marketed at BASF under the trade name ChemCycling®, and another is the BMB (biomass balance) approach, relying on certified renewable feedstocks, preferably derived from waste, residues, and other biogenic sources. Regardless of the version, the mass balance approach offers the important benefit of being scalable so that the “green” transformation can start with the small amounts of alternative feedstock available today, but can also grow seamlessly with the increasing availability of waste-based plastic or biomass-based feedstock.
Read on to learn all about Biomass balance approach (basf.com), Chemical recycling of plastic waste (basf.com) and how these concepts support the transformation towards a more sustainable future, not only in automotive production.
Overhauling the chemical value chain: fossil-free initiatives
BASF’s biomass balance, as well as the ChemCycling® approach, were spawned from a simple question: Could there be a way to replace the fossil feedstock for all the thousands of products manufactured in a huge, integrated and complex production network? The answer lies in sourcing alternative, non-fossil raw materials alongside existing conventional fossil feedstocks so early in the production chain that the final products remain unchanged chemically and thus offer the same performance and quality but have an impact on the overall greenhouse gas emissions.
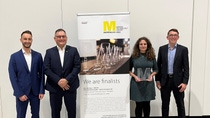
From theory to practice
A prominent example of the application of the mass balance concept is the Mercedes-Benz door handle (Interactive animation – Experiencing the mass balance approach (basf.com)). “In replacing fossil raw materials by pyrolysis oil on the one side and biomethane on the other, BASF was able to offer two mass-balanced products of the Ultramid® (polyamide) portfolio to the automotive value chain: Including in this case, next to Mercedes-Benz, the door handle supplier WITTE Automotive, explains Oliver Geiger, Senior Sustainability Manager, Performance Materials Europe, BASF.
With these two plastic materials, Mercedes-Benz is contributing to a reduction of plastic waste, a reduced product carbon footprint, and, in both cases, moving slowly away from fossil feedstock in the manufacturing of chemical products like plastics.
One Piece of the Puzzle - Complementarity
“One important aspect of our transformation approach is complementarity,” Reuber said. “This means mass balance is a very crucial but not the only way to reach the goal of GHG reduction and fossil feedstock replacement: In addition, we offer specific dedicated approaches where we supply bio-based products - with a measurable bio-content - and also products which contain mechanically recycled plastics, e.g., one specific polystyrene-based plastic material for the construction sector. All these different approaches are needed to reach the required transition. It is all part of our way of a Circular Economy.”
Mass balance: Well-known and widely adopted
BASF certainly can’t take credit for the origins of mass balance, as it’s quite an old concept that has been used across many industries, from wood/paper via agricultural products like oils and cotton to green energy. BASF experts believe that this attribution logic of circular/alternative feedstock must be effectively used by many value chains, not even restricted to the chemical industry but also including the metal producers and all downstream industries.
Bridging the gap with consumers and policymakers
“It’s important to describe and explain this sometimes not-so-intuitive mass balance approach to consumers but also to policy makers,” Reuber said. “The mass balance approach has a valuable impact by enabling to replace fossil feedstocks by more circular ones already today.” As countries begin mandating that circularity targets be met, an approach like mass balance is urgently needed to fulfill these targets. There are different ways to efficiently use plastic waste as a new feedstock, and there are different concepts to integrate biogenic sources as feedstock, thus contributing to options for CO2 emission reduction. For both feedstock alternatives, the chemical industry needs the Mass Balance approach as one way - not the only way - to replace conventional raw materials. It enables the attribution of these alternative feedstocks - combined with fossil feedstock – to specific sales products that are valued by the customers. This is especially crucial for the early phase of the transition.
Driving sustainable mobility - mass balance as a key enabler
The mass balance approach means shifting BASF’s input streams to increase use of circular or alternative raw material. This way, it can also shift the automotive industry’s sustainability efforts into high gear if the automotive value chain is willing to embrace alternative but impactful concepts like mass balance.
“The automotive industry – like all other industries depending on high-quality products – will certainly chose several different ways at the same time to achieve its climate protection goals,” Matthias Scheibitz, sustainability strategy manager at BASF’s Performance Materials division said. Electric vehicles are key for enabling a sustainable future of transportation. However, in the transition phase, companies need to be continuously exploring new ways to lower their carbon footprint when it comes to traditional ICE vehicles, too. “Mass balanced products can just as easily be applied to combustion engines as they can to electric vehicles. Their elegance lies in the combination of proven environmental benefits while keeping all product properties unchanged and thus not only complementing other GHG emission reduction concepts but enabling a seamless transition to a more sustainable future.”
It’s a time of unprecedented transformation in all value chains because this transformation encompasses all kinds of production.
For more on BASF’s mass balance approach, read The Mass Balance Approach (basf.com).