Automotive & Transportation
BASF's composite expertise means metal sits out for lincoln continental seat
Ford Motor Co. wanted to introduce an innovative seating architecture for the highly anticipated, all-new Lincoln Continental.
BASF contributed to a 20 percent weight reduction for the seat pan when compared to its metal predecessor
When overhauling the system, the automaker was looking to lightweight the front row seats in this iconic luxury vehicle, making the transition from metal to plastic material without sacrificing the inclusion of best-in-class comfort features.
BASF, a long-time strategic partner of Ford, leveraged its material and technical expertise to lightweight and optimize the design of the seat pan and exceed crash safety standards. The seating system as a whole was lightweighted by eight percent, but BASF contributed to a 20 percent weight reduction for the seat pan when compared to its metal predecessor. The project also resulted in a 15 percent cost savings.
The composite seating structure was awarded top honors during the Society of Plastic Engineers annual Automotive Innovation Awards Competition.
Material Selection and Meeting Crash Safety Metrics
With more than a decade of composite seating experience, BASF successfully incorporated its Ultramid® polyamide components into the new seat, including a nonmetal seat pan.
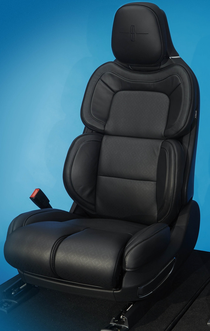
Several iterations of the seat pan - a significant component to meeting crash standards - had been created using different designs and materials. However, none were capable of withstanding the cold weather impact test. BASF recommended an impact resistant grade of its Ultramid polyamide that was 35 percent glass fiber reinforced and capable of withstanding the rigorous crash tests.
"This was a challenge because we were trying to meet the cold and hot performance metrics with a component that has historically been made of metal," said Matt Parkinson, senior applications development engineer for BASF. "The seat needed to perform under a broad range of assumptions, from the size and weight of a potential occupant to an environment of extreme cold and hot temperatures with varying humidity."
In addition, the benefit of using plastic, as opposed to metal in this application, is that the composite is able to absorb energy from the impact and flex without failing, returning to its original structure.
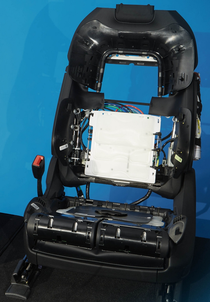
The 35 percent glass fiber reinforced material was denser than other material options; yet BASF was still able to lightweight the part by 20 percent because of its design optimization capabilities. The original pan was three separate injection molded pieces that were fastened together with six screws. It was redesigned into a single injection molded piece with strategically placed ribs to provide additional structural performance.
"The overall result was a 20 percent in weight reduction from the original component that Ford had been working with," said Jeffrey Hagar, market segment manager for automotive interiors for BASF's Performance Materials Division. "And through BASF's proprietary software ULTRASIM, we were able to analyze different design iterations without having to conduct a physical crash each time, which reduced costs."
By leveraging ULTRASIM, BASF was able to predict the material performance in everyday and crash situations with up to 95 percent accuracy. This improved correlation between simulated tests and physical results. The system also allowed the team to test different design iterations with confidence the final design would meet physical crash test standards.
"It was Ford's original request to find a partner that could demonstrate the correlation between the computer-aided engineering model and the physical results," said Mike Barry, OEM business development manager at BASF. "Our ULTRASIM technology offers best-in-class predictive modeling, which resulted in material and cost efficiencies and illustrates BASF's expertise in developing high performing composite seating solutions."
Lightweight Comfort
If reducing weight and cost wasn't enough, the use of a composite material also meant flexing some creative muscle to improve comfort.
The Continental's 30-way seat offers passengers the ability to adjust the lower cushion, seatback, headrest, upper-back support, thigh supports, lumbar support to their specifications for optimal comfort. These features would typically add a significant amount of weight had a composite material not been introduced.
The team was also able to use the analysis from ULTRASIM to do additional fine tuning for comfort, applying loads to the design to enhance quality and create special features such as the winged sections for additional thigh support.
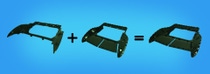
"Through the use of composite materials, we were able to help Ford achieve the new seat architecture that was lighter and more cost efficient. The Ultramid material checked all the boxes for a lightweight material that provides maximum performance," said Barry.